Decarbonization in Heavy Industries
In a world where reducing emissions and decarbonizing heavy industry by 2030 is crucial, Promecon's measurement technology presents a leading pathway to process optimization. Our company specializes in exhaust and airflow sensors, making a significant contribution to the transformation of heavy industry. Let's delve into how Promecon's advanced sensor technology helps minimize the industry's environmental impact and realize the vision of a low-carbon future.
The decarbonization of heavy industry is of paramount importance as historically, this sector has been responsible for substantial greenhouse gas emissions. To achieve ambitious climate goals, companies in heavy industry must find ways to make their production processes more environmentally friendly.
Our cutting-edge sensor technologies empower companies in heavy industry to streamline their processes and monitor emissions in real-time. This not only enables the identification of efficiency improvements but also ensures the timely detection of deviations or issues in the production process that could lead to unnecessary emissions.
Decarbonization in Steel & Smelting Industry
Sustainable decarbonization through advanced sensor technologies and research.
The steel and melting industry faces the challenge of optimizing its processes in line with global climate targets. Investing in advanced sensor technologies plays a crucial role in this. By using these technologies, the industry can collect accurate real-time data, leading to more precise control over emissions and energy consumption.
Investment in sensors and technology: Precise control for sustainable production. Industry should invest more in sensor technologies to monitor and optimize production. Advanced sensors enable up-to-the-minute data collection, which allows for more efficient use of resources and reduced emissions. These investments not only help to protect the environment, but also improve the competitiveness of companies through cost-efficient processes.
Research and development: Innovation-driven solutions for the future. Continuous research is essential to further improve sensor technologies. Innovative solutions can further reduce energy consumption and increase overall efficiency. Research projects should focus on developing sensors with higher accuracy and robustness to meet the specific requirements of the steel and melting industry
Regulatory compliance: ensuring environmental standards through technology. The industry must ensure that it complies with all applicable environmental standards and regulations. The use of sensor technologies plays a key role in this. By integrating sensors into production processes, companies can optimize their operations to meet strict regulations. This not only protects the environment, but also strengthens the trust of customers and business partners in companies' sustainability efforts.
Cooperation and knowledge exchange: synergies for a sustainable future. Collaboration with research institutes, other industries and government organizations is essential to share best practices and find innovative ways to further decarbonization. Joint projects and exchange of experience promote the development of new technologies and enable the industry to continuously improve.
By investing in advanced sensor technologies and actively participating in research, regulation and cooperation, the steel and smelting industry can not only make a significant contribution to decarbonization, but also sustain its competitiveness in a low-carbon future. The future of the industry lies in innovative and sustainable production driven by technological progress and close cooperation.
Exemplary carbon savings in an Electric Arc Furnace with PROMECON´s McON IR
|
|||
Furnace size: | 80 | tons | |
Electricity price (per kwh): | 0,23 | USD | |
Taps per day: | 25 | taps | |
Energy-savings per ton of steel: | 12 | kwh | |
Energy-savings per tap: | 960 | kwh | |
Energy-savings per day: | 24000 | kwh | |
Energy-savings 300 days: | 7200000 | kwh | |
|
10,416 | tons | |
|
3124,8 | tons | |
The key role of sensor technology in the steel industry is to increase efficiency and thus save energy.
-
Emission Control and Optimization: Sensors play a crucial role in measuring greenhouse gas emissions and pollutants during steel manufacturing, enabling real-time monitoring for emission reduction.
-
Gas Flow Optimization with Precision Sensors: High-precision gas flow measurements optimize energy use and process efficiency for steel decarbonization.
-
Efficient ID Fan Control: Sensors ensure efficient airflow management in blast furnaces, saving energy and reducing costs.
-
Accurate Furnace Exhaust Flow Measurement: Specialized high-temperature sensors accurately measure furnace exhaust flows, enhancing process control and reducing emissions.
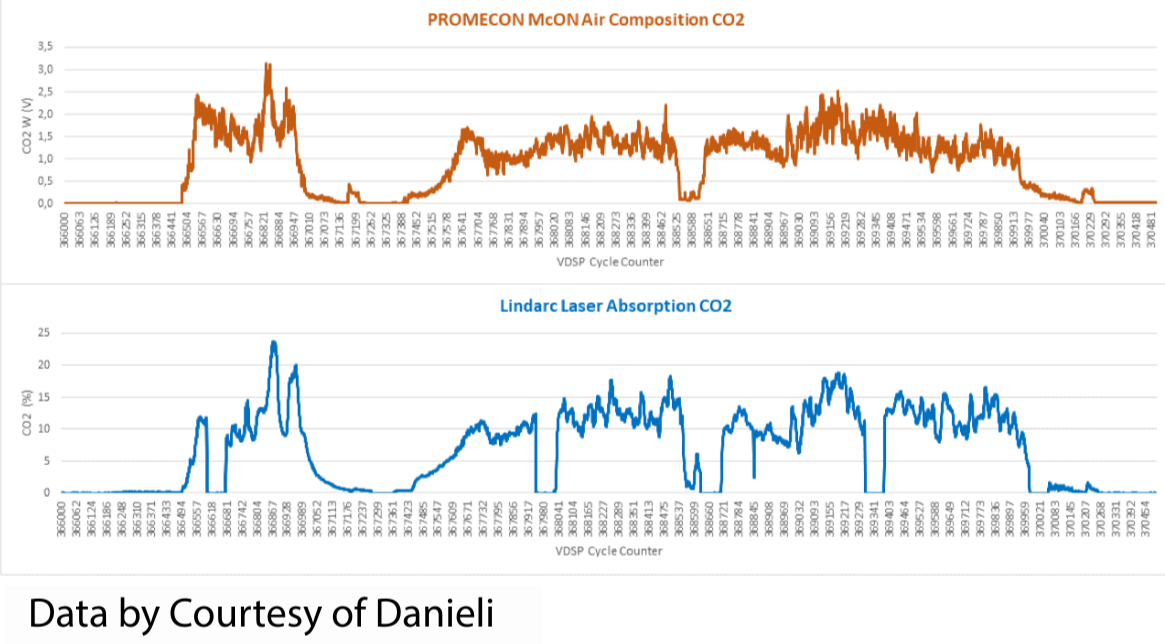
Decarbonization in Cement Industry
Action Required in the Cement Industry: Environmentally Friendly Production and Sustainability
The cement industry faces the challenge of minimizing its environmental impact and establishing sustainable production processes. Here are important measures and areas that the industry should consider to reduce its ecological footprint:
Explore and Utilize Alternative Raw Materials: The cement industry could explore and utilize alternative raw materials to reduce the demand for traditional materials. This step could not only decrease environmental impact from raw material mining but also contribute to a more sustainable production.
Investment in Advanced Sensor Technology: The cement industry should invest in state-of-the-art airflow sensors to achieve precise process control and energy efficiency. This investment leads to a more sustainable production process by minimizing waste and optimizing resource utilization.
Improve Energy Efficiency: By investing in energy-efficient technologies, process optimization, and renewable energy, the industry can reduce its energy consumption. This is crucial to lower CO2 emissions while simultaneously cutting operational costs.
Optimization of Calcination Processes: By implementing airflow sensors, the cement industry can optimize calcination processes, utilizing resources more efficiently and minimizing CO2 emissions. Precise control over these processes directly contributes to a greener production process.
Reduce Water Consumption: Implementing technologies to minimize water usage and utilizing water-efficient practices can significantly reduce water consumption. Water recovery systems and closed loops can help conserve water resources.
Optimize Waste Management: Efficient waste management involves better handling and recycling of waste products, reducing the need for landfills and minimizing the demand for new raw materials.
Research and Development for Innovation: Continuous research is crucial for enhancing sensor technologies and developing innovative solutions. This forward-thinking approach promotes environmentally friendly production methods, ensuring the industry stays at the forefront of sustainable practices.
Adhere to Environmental Certifications and Standards: Strict adherence to environmental certifications and standards is vital. The industry should ensure compliance with all applicable environmental regulations and potentially set voluntary targets for further reducing its environmental impact. Responsible action is key to a sustainable future.
Training and Integration: Proper training of employees is vital to effectively utilize sensor technology. Integrating these technologies seamlessly into the production process is critical for success. Well-trained staff ensures the optimal functioning of sensors, enhancing overall efficiency and reducing environmental impact.
Integrating Airflow Sensors in Cement Production for Decarbonization
-
Efficient Combustion Control: Airflow sensors ensure precise control of combustion air supply to the rotary kiln, optimizing combustion and reducing energy waste, which, in turn, lowers CO2 emissions.
-
Secondary Fuel Utilization: Airflow sensors contribute to efficient combustion of secondary fuels by regulating airflow precisely. This allows for the use of waste and biomass as substitutes for fossil fuels, reducing carbon emissions.
-
Calcinization Optimization: Accurate tertiary air control with airflow sensors stabilizes the calcination process, improving resource utilization and reducing energy consumption per ton of cement produced, ultimately reducing CO2 emissions.
-
Energy Savings: By precisely regulating fan systems and blowers, airflow sensors help reduce energy consumption in various parts of the production process, enhancing overall energy efficiency and lowering the CO2 footprint.
-
Preventing Energy Loss: Airflow sensors prevent unnecessary energy losses by ensuring that airflow is directed precisely where needed, reducing energy consumption and indirectly cutting emissions.
Power Industry
Driving Sustainability: Transforming Energy Landscape for a Low-Carbon Future
The urgent need to combat climate change and minimize our environmental impact demands a swift transition to sustainable energy sources and processes. In light of this, the energy industry must make a significant contribution to decarbonization. It is evident that fossil fuels need to be replaced to reduce CO2 emissions and create a low-carbon future.
Investment in Renewable Energy: The energy industry should invest heavily in renewable energy sources such as solar power, wind energy, and hydropower. These sources are not only environmentally friendly but also limitless and can ensure sustainable energy supply.
Research and Development: Continuous research is crucial to developing innovative technologies that enhance the efficiency of renewable energy systems and improve their integration into the grid. New storage technologies and smart grids are key elements for a reliable renewable energy supply.
Increase Energy Efficiency: Efficient energy production and usage are essential. The energy industry should invest in technologies that minimize energy loss and enhance the overall efficiency of energy generation and consumption.
Expansion of Infrastructure: A modern energy grid capable of integrating renewable energy sources is crucial. Investments in infrastructure, including smart grids and storage capacities, enable a seamless transition to renewable energies.
Education and Awareness: Public awareness about renewable energy and the importance of its utilization is paramount. The energy industry should initiate educational programs to raise awareness about sustainable energy options and promote societal acceptance.
By implementing these measures, the energy industry can make a significant contribution to accelerated decarbonization. The time to act is now. Through a concerted effort based on innovation, efficiency, and education, we can create a sustainable energy future and make significant progress toward a low-carbon world.
Sensor Technology's Role in Energy Sector Decarbonization, Specifically in Coal Power Generation and Combustion:
-
Primary Air Optimization: Sensors optimize the amount of primary air needed for combustion. Precise measurement and control of this airflow enhance combustion efficiency, reducing carbon emissions.
-
Coal Dust Flow: Sensors monitor and control coal dust flow, ensuring efficient coal combustion and preventing unnecessary emissions.
-
Secondary Air: Adding secondary air can improve combustion and reduce emissions. Sensors precisely control the quantity and timing of secondary air injection.
-
Excess Air Analysis: Sensors analyze excess air composition to monitor combustion quality. Efficient combustion minimizes pollutant emissions.
-
Burner Airflow Measurement: Precise sensors measure airflow in burners, ensuring optimal combustion, reducing fuel consumption, and lowering emissions.
-
Air/Flue Gas Flow: Sensors monitor air and flue gas flow to ensure efficient operation and prevent unwanted emissions.
-
Unburned Carbon Detection: Detecting unburned carbon in exhaust gases is vital for optimizing combustion. Sensors provide this information, enabling process optimization.